Gaswerk Herten
Herten im Jahre 1899, die Jahrhundertwende steht bevor, die Errungenschaften der Technik läuteten längst das Zeitalter der Industrialisierung ein. Damit war ein rasantes Bevölkerungs- und Städtewachstum verbunden. Der Ruf nach eine besseren Straßenbeleuchtung, die wirklich Sicherheit in der Dunkelheit gab, wurde immer lauter. Das konnte die spärliche Öllaternenbeleuchtung nicht gewährleisten, von denen im Jahre 1882 vier (!) Stück aufgestellt wurden. Daher beschlossen die Stadtverordneten den Bau eines Gaswerkes "zur Förderung der nächtlichen Sicherheit". Die Zeit der trüben "Funzeln" sollte bald vorbei sein.Das Gaswerk in Herten befand sich auf dem Gelände der heutigen Stadtwerke, an der Herner Str. 21. Das Grundstück konnte für 2000 M pro Morgen (= 2500 m2) erworben werden. Der Bau der Gasanlagen des Werkes stand unter der Obhut der Berlin-Anhaltische Maschinenbau Actiengesellschaft (BAMAG) Werk Berlin.
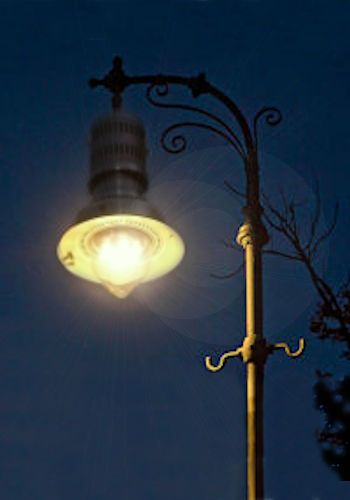
(©Fotosammlung Barz/Berg)
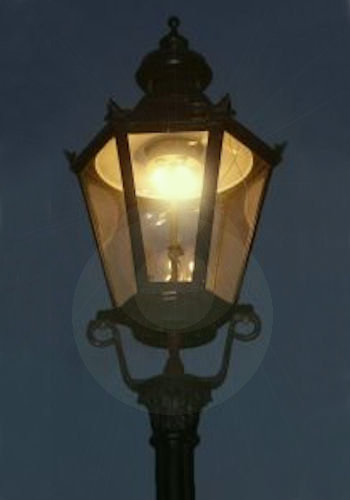
(©Fotosammlung Barz/Berg)
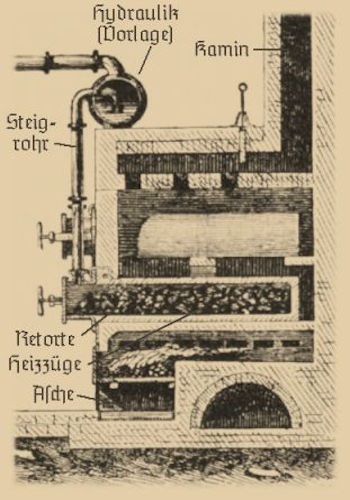
(Entnommen aus: Meyers Konversations-Lexikon,
Leipzig u. Wien, Vierte Auflage, 1885-1892)
Am 21. September 1900 teilte der Vorsitzende in einer Versammlung mit, daß die Gasanstalt fertiggestellt sei und die Eröffnungsfeier im Gastraum der Gasanstalt (Beamtenhaus) am 29. September 1900 um 17 Uhr stattfinde. Der Bau der Gasanstalt kostete insgesamt 188.688,04 M, veranschlagt wurden 196.800,00 M. Die Ersparnis wurde in Umwandlung der Straßenbeleuchtung investiert, in kostenfreie Gestellung der ersten Gasanschlüsse, Aufstellung von Gasmessern und Beschaffung von Gasuhren. Die Kandelaber für die Straßenbeleuchtung lieferte die Firma G. von Koepen aus Köln-Ehrenfeld zu einem Preis von 36,50 M pro Stück. Auch das Amtshaus erhielt in mehreren Räumen Gasbeleuchtung. Der Sitzungssaal, zwei Zimmer in der Wohnung des Amtmannes und auch das Büro wurden mit Gaslicht beleuchtet. Bereits im Jahre 1902 verfügte Herten bereits über 266 Gaslaternen in den Straßen.


Erste Ausbaustufe.
Das Gaswerk war zunächst für eine Gasproduktion von 1250 m3 in 24 Stunden ausgelegt, die Erweiterungsfähigkeit des Werkes war jedoch bereits eingeplant. Diese Ausbaustufe umfaßte im wesentlichen das Kohlenlager, Ofenhaus, Apparateraum (Raum für die Kühler (Kondensation)), Reinigerraum (hier befanden sich Reinigerkästen zur Entschwefelung), Uhr- und Reglerraum (Standort des Stationsgasmessers und Druckreglers), Regenerierraum (auch Regenerierschuppen genannt, Raum zur Aufbereitung der Reinigungsmasse), Arbeiterstube (Tisch, Bänke, Schränke und eine Kochgelegenheit für die Erwärmung der mitgebrachten Speisen), Baderaum, Werkstatt und Gasbehälter. Der Abort befand sich unweit dieses Gasometers.Um die Jahrhundertwende fiel fast sämtlicher Steinkohlenteer als Nebenprodukt bei der Leuchtgasherstellung an. Daher wurde er auch oft als "Gasteer" bezeichnet ebenso wie das ammoniakhaltige Kondensatwasser als "Gaswasser" und der Koks als "Gaskoks". Die nötige Gasförderkohle lieferte die Zeche Ewald. Die eigentliche Erzeugung des Leuchtgases geschah im Ofenhaus. Dort befanden sich die Gasöfen zur Vergasung der Kohle. In ihnen befanden sich die Retorten: gerade, am hinteren im Ofen liegenden Ende, geschlossene Röhren von knapp 3 m Länge, etwa 50 cm Durchmesser und von elliptischem Querschnitt (siehe Abbildungen). Die Retorten wurden indirekt mit Koks beheizt. Der Koks wurde auf einem Rost verbrannt und die Heizgase stiegen zwischen den von Pfeilern gestützten Retorten aufwärts bis zum Gewölbescheitel, zogen dann zwischen den Retorten und Gewölbewand links und rechts abwärts und gelangten unter den untersten Retorten auf dem Wege von vorn nach hinten in den Rauchkanal. Ein gut durchdachter Abhitzeweg der Rauchgase sicherte eine gleichmäßige Entgasung der Kohle. Die Beschickung dieser Retorten erforderte 150 kg Steinkohle, die in gleich große Stücke zerkleinert, rasch eingebracht und gleichmäßig ausgebreitet werden mußte. Nach der Entgasung mußte der Koks vor Einführung der neuen Ladung natürlich entfernt werden.
Die Arbeiten mußten akkurat und zügig ausgeführt werden; das Beschicken der Retorten geschah bis zum Jahre 1908 die Retorten manuell mit Schaufeln.
Die Leiter der Gasfabriken sahen fast immer in erster Linie darauf, aus der Kohle möglichst viel Gas zu gewinnen, und destillierten die Kohle daher bei möglichst hoher Temperatur.
Das Ablöschen des Kokses geschah ebenfalls im Ofenhaus selbst, nicht unter freiem Himmel wie auf einer Kokerei. Der entstehende Wasserdampf und die Rauchgase entwichen durch die sog. "Laterne" des Ofenhausdaches (Laternendach).
Die Gasausbeute betrug aus 100 kg Kohle etwa 32 m3 Gas. In einem Monat wurden im Schnitt aus 124 t Kohle etwa 39435 m3 Gas, 77120 kg Gaskoks und 16750 kg Teer erzeugt.
Vorlage (Hydraulik).
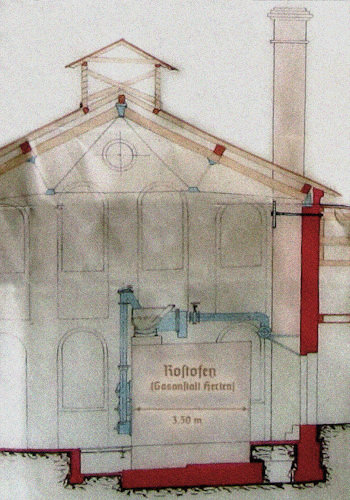
(© Stadtarchiv Herten)
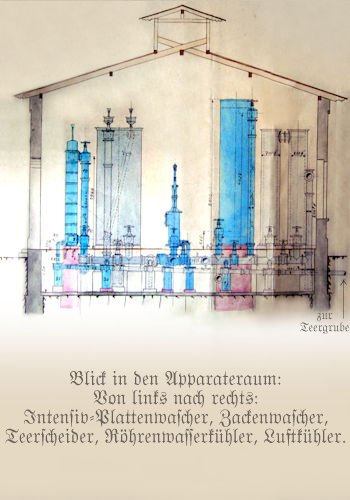
(© Stadtarchiv Herten)
Die Rohgase stiegen am vorderen Ende der Retorte dem sog. Mundstück durch das Steigrohr in die Höhe und mündeten über ein abwärts gerichtetes Tauchrohr in das Kondensat der Vorlage. Die Vorlage war an der Ofendecke hinlaufendes und allen Retorten eines Ofens, meist auch einer ganzen Ofenreihe, gemeinsames trogartiges Rohr, in dem ein großer Teil der unerwünschten Stoffe, Teer und Ammoniakwasser, niederschlugen. Dadurch wurde auch zugleich ein Wasserverschluß an der Mündung des Tauchrohres hergestellt, der ein Zurücksteigen des Gases in die Retorten während des Ausleerens und Neubeschickens verhinderte. Eine Anzahl in die Vorlage tauchender Putzrohre machten den Inhalt der Vorlage, auch während des Betriebes, zur Beseitigung der störenden Teerverdickungen zugänglich. Die Putzrohre waren, ebenso wie die Steig- und Tauchrohre, mit gasdicht schließenden Deckeln versehen. Das Reinigen der Steigrohre geschah manuell mit Bohrer und Schieber.
Kühler.
Nachdem in der Vorlage sich ein Teil des Rohteers niedergeschlagen hatte, gelangte das Rohgas in die Kühler. Zunächst passierte das Rohgas zwei Ringluftkühler, anschließend den Röhrenwasserkühler. Hier wurde das Gas von 75° C Vorlagetemperatur auf 12° 17° C Bodentemperatur abgekühlt damit weitere beigemengten Wasser- und Teerdämpfe kondensierten.Das sollte langsam geschehen, um Naphthalinverstopfungen zu vermeiden. Daher waren dem Wasserkühler zwei Luftkühler vorgeschaltet, in denen das Gas die Wärme an die umgebende Luft abgab. Um derart dem Gas die Wärme zu entziehen waren sehr große Flächen, also sehr große Kühler erforderlich. Das Gas passierte anschließend den Wasserkühler, der nach dem Gegenstromprinzip arbeitete. Der Röhrenwasserkühler war zylindrisch und durch zwei Zwischenböden in drei Kammern geteilt, die erste und unterste Kammer, die beiden sog. Wasserräume, standen durch eine Anzahl Röhren, (Kühlrohren) im Innern des Kühlers miteinander in Verbindung.
Durch die Röhren floß permanent kühles Wasser und das Gas verließ den Kühler
dort am meisten gekühlt, wo noch nicht gebrauchtes, kühles Wasser in den Kühler eintrat. Das Wasser trat in die unterste Kammer ein und
strömte durch die Kühlröhren zur oberen Kammer, wo es abgelassen wurde. Das Gas fiel dem ansteigenden Kühlwasser entgegen nach unten. So
wurde der Rest der Kühlung schnell und sicher erzielt, ohne die Leuchtkraft des Gases zu beeinträchtigen. Die Maße der Ringluftkühler betrug H=4 m
mit etwa 1 m Durchmesser. Das Kondensat sammelte sich auf dem Boden der Kühler.
Gassauger.
Die notwendige Gasbewegung wurde mittels eines Saugers durchgeführt, der durch einen 2 PS Gasmotor mit zwangsläufiger Ventilsteuerung und Glührohrzündung angetrieben wurde. Die Kraftübertragung zum Antrieb des Gassaugers erfolgte über Transmission.Ammoniakwascher.
Um dem abgekühlten Gase weiteres Ammoniak zu entziehen wurde es nun dem Doppelzackenwascher zugeführt. Dies war ein aufrechtstehender, gasdicht genieteter mit Zackeneinlagen versehener rechteckiger Blechkasten, geteilt in zwei Abteilungen. Im Gegenstromprinzip wurde das Ammoniak aus dem von unten aufsteigenden, fein zerteilten Gasstrom durch innige Berührung mit dem von oben herabströmenden Berieselungswasser fast völlig ausgewaschen.
Teer- und Ammoniakwassergruben.
Der Rohteer und das Ammoniakwasser wurde zu Hauptsammelstelle geleitet, den Teer- und Ammoniakwassergruben, die 1,5 m von dem Betriebsgebäude entfernt waren. Sie waren mit hölzernen, in Rahmen liegenden Deckeln dicht verschließbar abgedeckt, die mit kleinen Öffnungen versehen waren. Die Grube selbst waren in Ziegelmauerwerk gehalten und von innen mit Mörtel glatt verputzt.H2S-Reiniger.
Der Schwefelwasserstoff mußte aus dem Gase mit großer Sorgfalt entfernt werden, nicht nur wegen seiner giftigen und schädlichen Eigenschaften, sondern um die Bildung von schwefliger Säure bei der Verbrennung von schwefelwasserstoffhaltigem Gas zu vermeiden. Der Schwefelwasserstoff wurde in Reinigerkästen entfernt. In jedem waren 3 Lagen Raseneisenerze (Eisenoxydhydrat) als Reinigungsmasse auf Holzhorden etwa 30 cm hoch, locker aufgeschüttet, ausgebreitet.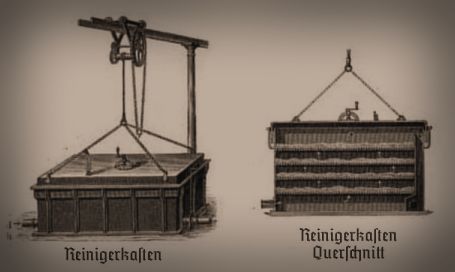
Bibliographischen Instituts, Leipzig u. Wien, Vierte Auflage, 1885-1892)
Die dabei eintretende Erwärmung wurde durch zeitweiligen Wasserzusatz in Schranken gehalten, damit nicht das Hydratwasser entweicht. Die Regeneration der Masse dauerte etwa 8 bis 14 Tage. Da der bei der Regenerierung entstehende elementare Schwefel nicht von der Reinigungsmasse abgetrennt werden konnte, ließ die Reinigungswirkung mit der Zeit nach und die Masse mußte nach etwa 10 Regenerationen ausgetauscht werden.
Gasuhr.
Das gereinigte Gas wurde nun, nachdem es hinsichtlich der Mengen in der Gasuhr gemessen wurde, in den für sich stehenden und mit Wasserfüllung vorgesehenen Gasbehälter geführt.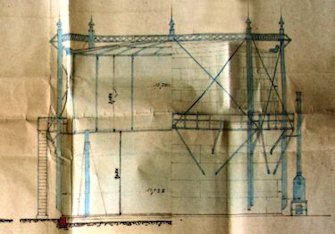
(© Stadtarchiv Herten)
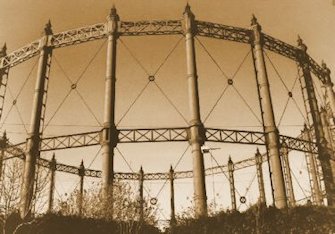
(© Website Dublin Gasworks)
Gasbehälter.
Der Glockengasbehälter, auch nasse Gasbehälter, diente als Gasspeicher, da der Gasbedarf der Stadt Schwankungen unterlag. Nicht nur über einen Tag unterschied sich der Verbrauch, sondern auch zwischen Sommer und Winter. Der Verbrauch war keine konstante Größe, sondern schwankte ständig um einen Mittelwert, während das Gaswerk meist kontinuierlich produzierte.Der Gasbehälter selbst, mit einem nutzbaren Inhalt von 1000 m3, bestand aus einer gasdicht genieteten, unten offenen, oben mit kugelförmiger Decke versehenen, schmiedeeisernen Glocke, die im einen schmiedeeisernen, wasserdichten Bassin schwamm. Wurde mehr Gas erzeugt, als abgegeben, so hob sich die Glocke und das Gas sammelte sich in dem Behälter, wurde weniger Gas erzeugt als abgegeben, so sank die Glocke.
Größtes Augenmerk galt dem Führungsgerüst mit den Führungsböcken, damit sich die Glocke bei ihrer vertikalen Bewegung sicher gleiten und ein Kippen oder Verkanten der Glocke ausgeschlossen werden konnte, selbst beim Höchststand der Glocke. Ebenso wurde sorgfältig darauf geachtet, daß die Glocke immer genügend in das Wasser des Bassins eingetaucht war, sodaß ihr Inhalt vollständig vom Äußeren abgeschlossen und keine Gefahr des Entweichens von Gas bestand. Um den Gasbehälter vor Witterungseinflüsse zu schützen war er mit Mauerwerk verkleidet. Das Wasser im Bassin, das auch Schmierstoffe enthielt, war beheizbar um ein einfrieren in der Wintermonaten zu verhindern.
Stadtdruckregler.
Ehe das Gas aus dem Gasbehälter in die Stadt zugeführt wurde, durchströmt es den Stadtdruckregler. Dieser Apparat bestand aus einem Wassergefäß mit Schwimmerglocke und Ventil und dient dazu, den Druck, mit welchem man das Gas in die Stadt schickte, zu regulieren.
Transport und Verkauf der "Nebenprodukte".
Der Gaskoks wurde im geschlossenen Raum abgelöscht und dann im Freien bis zum Verkauf aufgeschüttet. Der Teer und das Ammoniakwasser wurden in den entsprechenden Gruben gelagert um anschließend in Holz- oder Eisenfässer (Fassungsvermögen etwa 255 kg Teer) gefüllt und versandt zu werden. Diese Methode des Transportes war arbeitsaufwendig und unwirtschaftlich. Nicht nur die Hinfracht der leeren Fässer schlug zu Buche sondern auch bei der Rückfracht das Taragewicht der gefüllten Fässer. Dies senkte die Attraktivität des Produktes bei potentiellen Käufern, obwohl der Teer von kleineren Betrieben oft qualitativ besser war.Erweiterung 1907.
Schon bei der Planung des Gaswerkes wurde eine Erweiterung der Gasanstalt in Betracht gezogen und mit eingeplant. Mit Erbauung eines zweiten Gasbehälters und eines weiteren Gasofens könnte mit geringem Aufwand die Gasproduktion auf 2500 m3 in 24 Stunden gesteigert werden. Nicht nur zur Ausbau des Gaslichtnetzes ließen den Gasbedarf steigen. Zwar wurde die Gasbeleuchtung in Innenräumen ab 1910 von der aufkommenden Elektrizität verdrängt, dafür gewann das Stadtgas an Interesse zu Koch- und später und auch zu Heizzwecken bei den Konsumenten.Erweiterung der Ofen- und Apparateanlage.
Der Ausbau umfaßte die Errichtung eines neuen VIIIer Generatorofens, den Umbau eines vorhandenen VIer Rost-Ofens in einen Generator-Ofen, die Aufstellung eines schmiedeeisernen Röhrenwasserkühlers, eines Gassaugers mit Umlaufregler, eines Gasmotors, eines Teerscheiders, eines Intensiv-Plattenwaschers, dem Belegen der vorhandenen 3 Reiniger mit Reinigereinbau Typ BAMAG, die Unterbringung der Werkstatt in einen Neubau (Grundfläche 12 m x 6 m) und die Vergrößerung des Regenerierschuppens.Mit der Erweiterungsmaßnahme der Gasreinigung und der Ofenanlage konnte die tägliche Produktion auf 4000m3 gesteigert werden.
Generatoröfen.
Die Leistungsfähigkeit der Retorten-Ofenanlage wurde dadurch vergrößert, daß einmal ein ganz neuer Generatorofen mit 8 Retorten im Anschluß an den vorhandenen Ofenblock errichtet und der vorhandene VIer Rost-Ofen in einen Generatorofen umgewandelt wurde. Die Generator- oder Gasfeuerung bezweckte eine höhere Entgasungstemperatur für eine höhere Gasausbeute zu erreichen, denn das war bei der Rostfeuerung (ohne Regeneratoren) nicht möglich, weil bei ihr die Verbrennung mit einem Überschuß von Luft, der kühlend auf die Heizgase wirkte, gearbeitet wurde.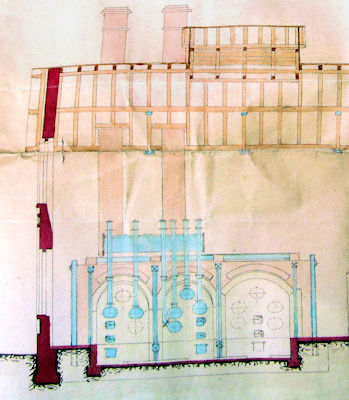
Bei den Rostöfen wurde der Koks auf einem Rost verbrannt und die Heizgase stiegen zwischen den von Pfeilern unterstützten Retorten aufwärts bis zum Gewölbescheitel, zogen dann zwischen Retorten und Gewölbewand links und rechts abwärts und gelangten unter den untersten Retorten auf dem Wege von vorn nach hinten in den Rauchkanal.
(© Stadtarchiv Herten)
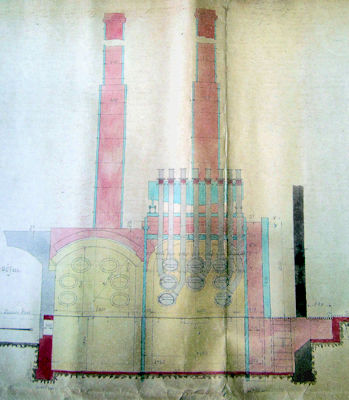
Der Generatorofen wurde mit Gas befeuert, um eine vollkommenere Verbrennung des Brennmateriales herbeizuführen. Das war bei Rostfeuerung nicht möglich, weil bei ihr die Verbrennung mit einem Luftüberschuß erfolgte, der kühlend auf die Heizgase wirkte. Im Generator wurde unter beschränkter Luftzuführung (Primärluft) Kohlenmonoxid erzeugt, das beim Eintritt in den Ofen mit Sekundärluft verbrannte.
(© Stadtarchiv Herten)
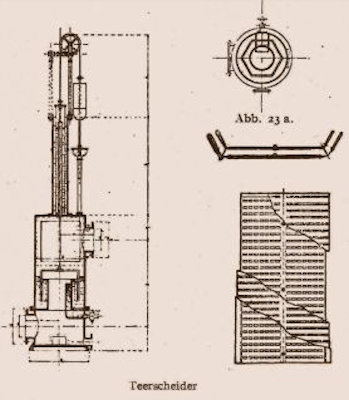
In diesem Apparat wurden die feinen Tröpfchen Teer mit Hilfe von versetzt eingesetzten Lochblechen in einer Glocke aus dem Gas abgeschieden. Der Teer floß an den Wänden der Glocke herab während das Gas durch ein anderes Rohr ausströmte.
(Handbuch der chemischen Technologie;
Direktor Th. Beckert [u.a.], 1895)
Im Generator wurde unter beschränkter Luftzuführung (Primärluft), die eine unvollständige Verbrennung bewirkte, ein Gemisch aus ca. 25 % Kohlenmonoxid und 70 % Stickstoff (Generatorgas auch Luftgas) erzeugt. Dieses Generatorgas wurde beim Eintritt in den Ofen mit Luft (Sekundärluft) gemischt und verbrannte mit blauer Flamme zu Kohlenstoffdioxid. Der Generator lag unter dem Fußboden im Gewölbe unter den Retorten, wobei das Generatorgas durch Schlitze in den Heizraum trat. Der zu verbrennende Koks lag im Generator auf einer Schamottesohle, die seitlich mit Schlackenschlitz versehen war. Die Sekundärluft wurde in einem Regenerator, der den unteren Teil des Ofens ausfüllte, erwärmt und dem Generatorgas, sobald es in den Heizraum trat, zugeführt. Die abziehenden Heizgase wurden mittels einer Anzahl Kanäle zunächst durch den Regenerator geführt, wo sie einen großen Teil der enthaltenen Wärme an die Sekundärluft abgaben, um dann in den Schornstein zu treten. Die für eine gute Wirkung des Ofens wichtige Regulierung der Menge zuzuführender Sekundärluft geschah an deren Eintrittsstelle in den Regenerator durch Luftschieber. Innerhalb so eines Ofens konnten 900 kg Kohle in 24 Stunden zu 252 m³ Gas und 567 kg Koks verarbeitet werden, wobei eine Kohlenbefüllung rund 4 bis 6 Stunden zur Entgasung benötigte.
Teerscheider Pelouze.
Das Leuchtgas enthielt ziemliche viele Teerbestandteile in Form feinster Tröpfchen. Zum Teil verdichteten sie sich in den Gasleitungen, und wurden sowohl in den Gasfabriken selbst als auch in den "Siphons" der Stadtleitungen als Öle oder als feste Naphthalinausscheidungen gesammelt. Denn alleine eine Kühlung des Gases konnte keine gänzliche Ausscheidung des Teeres gewährleisten. Daher wurde ein Teerscheider aufgestellt, um eine bessere Befreiung des Rohgases von Teerteilchen zu erreichen.Im innern des Teerscheiders war eine zerlegbare Glocke freischwebend aufgehängt, an ihrem unteren Rande tauchte sie in der Flüssigkeit der innen liegenden Tasse. Dadurch war sie hydraulisch abgeschlossen. Das Gewicht der Glocke wurde durch ein Gegengewicht ausgeglichen und durch den Regulator konnte sie auf einen bestimmten Druck eingestellt werden.
Das eintretende Gas gelangte nun in den Innenraum, durchstrich die Glocke, deren Wände aus 2 bis 4 konzentrischen Blechen mit feinen, in den verschiedenen Schichten verschieden gestalteten Öffnungen bestand. Diese waren so angeordnet, daß jeder Öffnung in dem einen Blech die geschlossene Wand in dem nächsten gegenüberstand, wodurch das aus dem Innern der Glocke tretende Gas aufs feinste verteilt und mehrfach an die Blechwandung anstieß. Die feinsten Teertröpfchen verdichteten sich so zu größeren Tropfen, liefen die Wand hinab und sammelten sich unten an, wo sich ein Abfluß befand. Von Teer befreit verließ das Gas die Glocke mittels eines Rohres.


Intensiv-Plattenwascher.
Dieser Wascher war hinter dem vorhandenen Ammoniakwascher (Doppelzackenwascher) geschaltet. Er bestand aus einzelnen Etagen, in welchen herausnehmbare Plattenpakete untergebracht waren. Diese vertikalen Plattenbündel bestanden aus einer Anzahl von Blechen, die in geringen Abständen voneinander gelagert waren. Zwischen diesen Plattenbündeln stieg der Gasstrom in den Apparat empor. Gleichzeitig wurden die Pakete von oben mit Wasser berieselt, sodaß der Gasstrom durch die schmalen Bleche in hin- und hergehender Richtung verteilt und dabei intensiv gewaschen wird, wodurch das Ammoniak bis auf Spuren entfernt wurde.Reinigereinbau "BAMAG" D.R.P.
für trockene Gasentschwefelung.
Durch die zukünftige Verwendung von den Reinigereinbauten BAMAG in den Reinigerkästen, in denen das Gas von Schwefelwasserstoff und Kohlensäure befreit wurde, konnte deren Leistungsfähigkeit erhöht werden. Bei dieser Einrichtung wurde der Gasstrom geteilt, sodaß das Gas mit halber Geschwindigkeit wie sonst, durch die Reiniger strich, außerdem konnte fast doppelt so viel Reinigungsmasse in jedem Kasten eingebracht werden. Nach Belegen der Reiniger mit dem BAMAG-Einbau reicht aus, um 4000 m³ Gas in 24 Stunden von Schwefelwasserstoff und Kohlensäure vollständig zu reinigen.Im Jahre 1908, ein Jahr nach diesem Umbau, erfolgte die Errichtung eines zweiten Gasbehälters, eines Spiritusverdampfers, eine Erweiterung der Regleranlage,, eine Ladevorrichtung für die Beschickung der Retorten und eine Erweiterung des Uhrenraumes. Ferner wurde ein Kesselhaus mit Kesselanlage und Kamin für den Betrieb einer Dampfmaschine errichtet.
Zweiter Gasbehälter.
Der Gasbehälter mit den Maßen: Beckendurchmesser 17,8m und 7,1 m Höhe, Durchmesser der Glocke 16,8 m und 6,9 m Höhe, war von 1500m3 auf 3000m3 teleskopierbar, d. h. er war mit mehreren ineinander verschachtelten, zylindrischen Segmente ausgestattet, die teleskopartig wie bei einem Fernrohr ein- und ausgefahren werden konnten. Bei Füllung des Gasbehälters mit Gas hob sich zunächst die Glocke und danach ein Segmente nach dem anderen aus dem Wasser heraus. So konnte bei gleicher Bassingröße mehr Gas im Behälter gespeichert werden.Spiritusverdampfer.
Um ein des Verstopfen der Rohrleitungen und Laternen durch Gefrieren der sich aus dem Gase niederschlagenden Flüssigkeiten zu verhindern wurden nach dem patentierten Verfahren von J. Bueb dem Gas beim Austritt vom Stadtdruckregler in das Hauptrohr Spiritusdämpfe zugeführt. Denaturierter, 92 95 prozentiger Spiritus wurde aus dem Transportfaß in einen kleinen hochstehenden Behälter gepumpt und aus diesem durch einen mit Meßzylinder versehenen Zuflußregler dem Verdampfer, der im Reglerraum aufgestellt war, zugeführt. Dieser bestand aus einfachen, durch Gas geheizte Rohre, die dann mit Rücksicht auf die Feuergefährlichkeit der offenen Flamme im Arbeiterraum aufgestellt war. Je nach dem Kältegrad der Außenluft waren für 1 m3 Gas 4 8 g Spiritus erforderlich.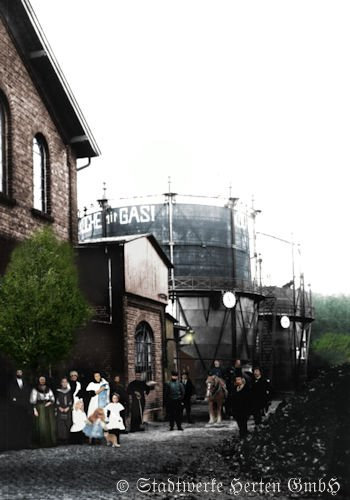
alle möchten auf das Bild.
Auf dem Gasbehälter motiviert ein Schriftzug
mit Gas zu kochen.
(© Stadtwerke Herten GmbH)
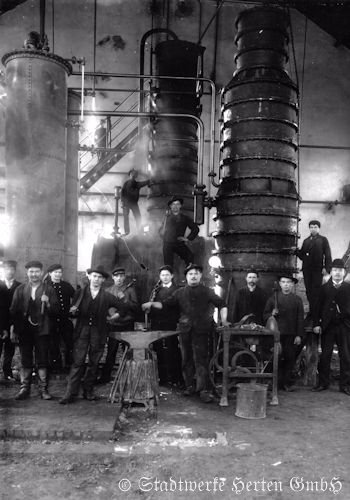
Links im Hintergrund die Luftkühler,
rechts die Ammoniakwascher um 1900
(© Stadtwerke Herten GmbH)
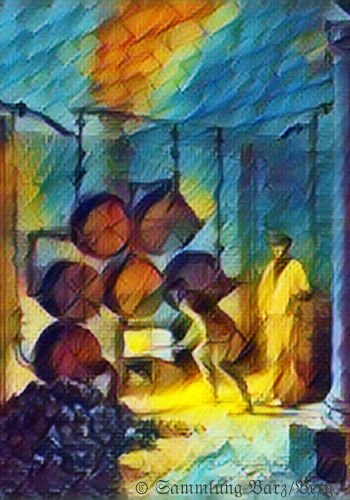
(© Sammlung Barz/Berg)
Erweiterung der Regleranlage.
Der vorhandene Regler wurde gegen einen größeren Regler System LEDIG für 1000 m³stündliche Gasabgabe einschließlich Sicherheitsregler aufgestellt.Erweiterung des Uhrenraumes.
Für die Unterbringung des neuen Reglers und der noch zu beschaffenden, größeren Gasuhr wurde der Uhrenraum um 4,80 x 3,01 m erweitert werden.Ladevorrichtung für die Beschickung der Retorten.
Zur schnelleren Beschickung der Retorten wurden nun endlich Lademulden eingesetzt, die eine ganze Ofencharge fassen konnten und von drei Arbeitern bedient wurden. In dem Ofenhaus und im Kohlenschuppen wurde eine Hängebahn eingerichtet, auf der sich eine Laufkatze befand und die Mulden bewegte.Kesselhaus mit Kesselanlage und Kamin
für den Betrieb einer Dampfmaschine.
Für den Antrieb der Gassaugeranlage, Ammoniak- und Teerpumpen war der Gasmotor mit 2 PS bald nicht mehr ausreichend, zudem sich auch keine Maschine in Reserve befand. Daher wurde eine einzylindrige Dampfmaschine beschafft. Der Zylinderdurchmesser betrug 150 mm mit 200 mm Hub und 3 PS. Der Antrieb erfolgte an der vorhandenen Betriebswelle mit Transmission. Um die Dampfmaschine mit Dampf versorgen zu können wurde auch ein Kesselhaus, ein Anbau von der Größe 11,50 m x 4 m an das Ofenhaus, mit einem Dampfkessel errichtet, sowie einem Kamin zur Abführung der Rauchgase von 25 m höhe un einen oberen lichten Durchmesser von 70 cm. Der Dampfkessel versorgte nicht nur die Dampfmaschine mit Dampf sondern auch den Apparaten-Raum mit Wärme und sorgte für die Beheizung des Wassers in den Gasbehältern, um ein einfrieren in kalten Wintermonaten zu verhindern. Die Heizfläche betrug 30 m² und 6 Atm. Überdruck.Arbeitsbedingungen.
Die Arbeit im Gaswerk war sehr schwer, laut und dreckig. Kohlenstaub, Rauchgase, die Hitze an den Öfen und das in einem geschlossenen Ofenhaus, waren kaum ideale Arbeitsbedingungen. Insbesondre beim leeren der Kammer und befüllen mit frischer Kohle war die Qualmbelästigung enorm.Die Arbeitszeit an betrug im Schnitt 10 Stunden. Die Arbeitskleidung an den Öfen bestand aus ausrangierter Straßenkleidung, Schutz boten nur Filzhüte und Holzschuhe, wie es auch auf Kokereien und auch im Hüttenwerk üblich war. Auffällig waren die gering dimensionierten Sozialräume. Eine Arbeiterstube mit den Ausmaßen 3,32 x 2,5 m, sowie einer kleinen Badestube, die nur eine Badewanne aufnehmen konnte. Einen Brauseraum für die Arbeiter gab es nicht. Die Arbeiter wuschen sich in Waschbrunnen oder -rinnen aus Steingut. Die Arbeitshygiene ließ daher zu wünschen übrig. Besserung brachte der Umbau um 1907, die Werkstatt wurde umgesiedelt in einen Neubau und der entstandene Raum zur Badestube umgenutzt, der alte, winzige Baderaum entfiel.
Wahrscheinlich auch auf Grund der sehr schwierigen Arbeitsbedingungen auf der Gasanstalt war das Arbeitsklima auf einem Gaswerk sehr gut und kameradschaftlich, wie viele ehemalige Gaswerker berichteten. Die Arbeit in einem Ofenhaus, das Herz eines jeden Gaswerkes, blieb stets für Außenstehende verborgen. Es war ebenso verbotenes Terrain wie bei einer Kokerei und Hüttenwerk.
Schließung des Gaswerkes.
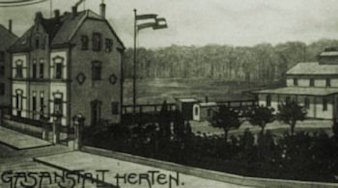
(© www.hertener-stadtwerke.de)
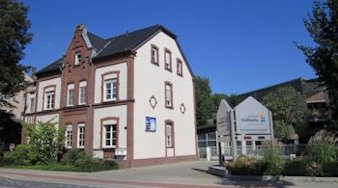
(© Michaela Barz-Berg, Fotosammlung Barz/Berg)
Das Gaswerk wurde wegen mangelnder Wirtschaftlichkeit im Jahre 1915 stillgelegt. Die technischen Verbesserungen auf den zahlreichen Kokereien des Ruhrreviers ermöglichten immer mehr Überschußgas zu erwirtschaften, denn immer weniger Koksgas mußte für die Unterfeuerung der Öfen verwandt werden. Regenerativ-Koksöfen verdrängten nach und nach die herkömmlichen Abhitzeöfen und im Oktober 1912 wurde die erste Verbundkoksofen-Batterie von Koppers erfolgreich in Betrieb genommen. Auf der Zeche Scherlebeck waren zur dieser Zeit (Schlägel und Eisen Schacht 5/6) 60 Collin Abhitze-Koksöfen und 124 Collin-Regenerativkoksöfen mit Nebenproduktengewinnung in Betrieb und auf Zeche Ewald Fortsetzung wurde ab 1911 auf der Schachtanlage 1/2 eine Kokerei mit Nebenproduktengewinnung betrieben.
Schon ein Jahr zuvor konnte die Gesellschaft des Gaswerks Herten ihren Versorgungsauftrag für die Stadt Herten erweitern und sorgte fortan nicht nur für Gas sondern auch für Strom und führte den Namen: "Gas- und Elektrizitätswerk Herten". Später wurde daraus die "Kommunale Wirtschaftsbetriebe GmbH Herten". Heute sorgen die Stadtwerke nicht nur für Gas und Strom sondern auch für Fernwärme.
Quellennachweis:
- Dr. A. Spilker, Generaldirektor der Gesellschaft für Teerverwertung Duisburg-Meiderich: "Kokerei- und Teerprodukte der Steinkohle", vierte Auflage, 1923
- Lueger, Otto: Lexikon der gesamten Technik, 2. Auflage 1904 1920
- Handbuch der chemischen Technologie; unter Mitwirkung von Direktor Th. Beckert [u.a.], 1895
- Dr. Otto Grosskinsky: "Handbuch des Kokereiwesens", Bd. I und II, Düsseldorf 1958
- Lunge, Georg: Die Industrie der Steinkohlentheer-Destillation und Ammoniakwasser-Verarbeitung, Braunschweig Vieweg Verlag 1899
- Dr. Winter, H. Hrsg., Taschenbuch für Gaswerke, Kokereien, Schwelereien und Teerdestillation, Verlag Wilhelm Knapp, Halle (Saale), 1950
- https://www.stadt-neukalen.de/verzeichnis/objekt.php?mandat=84694
- https://www.gaswerk-augsburg.de/
- Akten zum Bau der "Gasanstalt der Gemeinde Herten", AH 1136, AH 397; Stadtarchiv Herten
© Michaela Barz-Berg
Bild- und Textmaterial sind urheberrechtlich geschützt. Alle Rechte vorbehalten. Die Verwendung der Texte, Bilder oder Graphiken - auch auszugsweise - ohne Genehmigung des Webmasters ist strafbar.
Ich danke Herrn Maik Leppak, Stadtarchiv Herten
sowie Frau Petra Hertel, Stadtwerke Herten, für das Fotomaterial