Die Brikettierung
Etwa im ausgehenden 18. Jahrhundert begann man das Kohlenklein mit Lehm oder Ton als Bindemittel manuell zu sogenannte "Klüten" zu formen. Diese Art der Brikettierung war vor allem in der Rheingegend verbreitet. Eine nennenswerte Herstellung von Briketts begann in Deutschland erst etwa um 1880. Bis dahin galt die Verkokung als die wirtschaftlichste Verwendung des feinkörnigen Steinkohlenanfalles.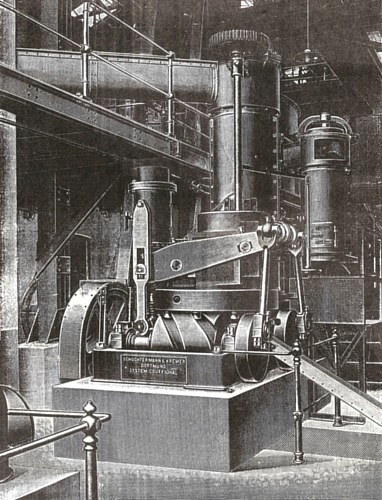
(© Sammlung Barz/Berg)
Aber genau dieses Pech verhinderte seinerzeit die Ausbreitung der Brikettierung in Deutschland. In England und Belgien dagegen faßte die Brikettierung 20 Jahre eher Fuß. Pech mußte daher teuer aus England importiert werden. Die Ursache hierfür lag in dem Mangel von Kohlenwertstoffgewinnungsanlagen (KWA) auf deutschen Kokereien. Erst nachdem immer mehr Kokereien mit KWAs ausgerüstet wurden, fiel auch das Pech in Deutschland in genügenden Mengen an. Damit wurde die Brikettherstellung auch für die hiesigen Zechengewerkschaften lukrativ.
Das Steinkohlenteerpech ist ein Rückstand der Teerdestillation. Seine Menge beträgt etwa 50 - 55 % des Rohteers. Man unterscheidet Weich-, Brikett- und Hartpech. Weichpech erweicht schon bei 40° C, Brikettpech bei etwa 60° C und schmilzt bei 70° C, Hartpech erst zwischen 70° - 90° C. Das Hartpech ist so spröde, daß es sich sogar an heißen Sommertagen in Stücke von muscheligem Bruch zerschlagen ließe.
An dieser Stelle möchten wir das Brikettierverfahren Anfang des 20. Jahrhunderts betrachten. Zunächst wurde das heiße, flüssige Pech in leichte Fässern gefüllt, wo es nach der Abkühlung erstarrte. Per Bahn wurde es so der Brikettfabrik angeliefert. Um Pechmangel durch Unregelmäßigkeiten in der Lieferung vorzubeugen verfügte jede Brikettfabrik über einen Mindestbestand an Pech im Pechkeller. Die Fässer wurden von dem Pech heruntergeschlagen und das Pech anschließend mit schweren Hämmern vorzerkleinert. Mit Schubkarren wurde es zu dem im Pechkeller aufgestellten Brecher gebracht, dort grobkörnig zerkleinert und dann im daneben befindlichen Pechknackwerk fein gemahlen, bevor es im Pechbunker eingelagert wurde. Die angelieferte Brikettierkohle aus der Wäsche setzte sich in etwa aus 65 % gewaschener und 35 % ungewaschener Feinkohle zusammen. Die nächste Aufgabe bestand nun darin, die Kohle und das Pech im richtigen Verhältnis gleichmäßig zu mischen. Der Pechzusatz betrug 6,5 %. Die Einbringung des Peches erfolgte i.d.R. durch Tellerdosierung. Hierfür befand sich unter dem Kohlenbunkertrichter mit seitlichem Auslauf ein gußeiserner Drehtisch, ebenso unter dem Pechbunker. Die auslaufende Pech- und Kohlemenge konnte durch Absperrschieber geregelt werden. Ein Abstreicher strich das Gut über den Rand der Teller in die Förderschnecke. Nun wurde das vermischte Brikettiergut zur Wärmebehandlung im Wärmofen transportiert. In diesem aus feuerfesten Steinen gemauerten Ofen befand sich ein gußeiserner Teller, der sich mit Hilfe einer Welle drehte. Die Umdrehungszahl richtete sich nach der Tourenzahl der Presse. Auf ihm befand sich ein feststehendes Rührwerk mit Rührwerkleisten wie Rechen. In der Mitte befand sich der Eintrag für das Brikettiergut. So wurde die Mischung gut durchgearbeitet, seitliche Streichleisten verhinderten dabei, daß das Korn vorzeitig vom Teller herunterfiel. Der Abstreicher führte die erwärmte Masse dem Austrag zu. Mit einer Transportschnecke wurde die nun gut durchgemischte und erwärmte, plastische Masse der Presse zugeführt.
Die Couffinhal-Presse des Unternehmens Schüchtermann & Kremer (SK), Dortmund, ist wohl die bekannteste Brikett-Presse, nicht nur, weil sie die verbreitetste war, sondern auch, weil sie die besten Ergebnisse erzielte. Nach der Pariser Weltausstellung 1878 erwarb SK das Patent dieser Presse, klug vorausschauend, daß die Brikettierung auch in Deutschland bald Einzug halten wird. Bis 1898 war das Unternehmen konkurrenzlos auf dem deutschen Markt und errichtete bis 1956 insgesamt 75 Brikettfabriken.
Die Couffinhal-Presse arbeitete mit zweiseitiger Pressung, d. h. das Brikettiergut wurde in die Mulde des Formtisches gefüllt und dann zwischen die Druckstempel gebracht. Diese Druckstempel waren mit dem Preßhebel verbunden. Mittels Kurbelscheiben, die über einer Vorgelegeachse mit dem Zahnrad verbunden waren, wurde der Preßhebel mit Hilfe einer Lenkstange auf und niederbewegt. Zu Beginn des Preßprozesses wurde die Pressung nur von dem oberen Stempel ausgeübt. Erst nachdem die Brikettmassen dem weiteren Zusammendrücken einen gewissen Widerstand entgegensetzten, wurde das Brikett auch von unten gepreßt. Die Vorgehensweise ist folgende: Durch den Widerstand des Briketts muß der Preßkopf in Ruhe verbleiben, dadurch wird bei weiterem einwirkendem Druck der Drehpunkt des Hebelsystems verschoben. (der Preßkopf wird ja durch die Druckstange noch tiefer herabgezogen!) Der untere Preßhebel mit dem Preßkopf vollendet nun von der Unterseite die Pressung. Danach wurde die Formplatte mittels der Führungswalze von neuem umgesetzt und ein neuer Preßvorgang in den benachbarten Formen begann. Die bereits fertigen Briketts verblieben in ihren Formen noch über eine halbe Umdrehung der Formplatte. Dann wurden sie von dem Ausstoßstempel, der mit dem oberen Preßstempel verbunden war, automatisch ausgestoßen. Über eine federnde Klappe fielen sie auf eine Ablaufrutsche. Fehlbriketts wurden bei der Verladung von Hand aussortiert.
Die gebräuchlichste Größe der Briketts war 220 * 110 * 105 mm, das entsprach einem Gewicht von 3 kg. In der Minute erfolgten 35 Pressungen. Eine Brikettfabrik mit einem Wärmofen und zwei 3-kg-Couffinhal-Pressen konnte 240 t Briketts am Tag produzieren. Der Heizwert der Steinkohlenbriketts liegt mit etwa ca. 8,7 kWh/kg wesentlich höher als der der Braunkohlenbriketts mit 5,4 kWh/kg. Holz hat nur rund 4,1 kWh/kg (trocken). Die für eine Brikettfabrik notwendige Investition (ohne Bauland) betrug um die Jahrhundertwende 135.000 ℳ, wobei eine 3kg-Couffinhal-Presse mit einem Preis von etwa 32.000 ℳ zu Buche schlug (1903).
Steinkohlenbriketts werden heutzutage ausschließlich als Eierbriketts hergestellt, deren Beliebtheit ab 1910 ständig wuchs. Am 31. März 2008 schloß die letzte Brikettfabrik in Deutschland nach 86 Jahren, die zuletzt 62 Mitarbeiter beschäftigte. Die SJ Brikett- und Extrazitfabriken GmbH war auf dem Schachtgelände der ehemaligen Zeche Sophia-Jacoba an der Horststraße in Hückelhoven ansässig. Ihre Briketts zeichneten sich durch erstklassige Qualität aus und waren leicht an den eingeprägten Buchstaben S zu erkennen. Bekannt wurde die Hückelhovener Brikettfabrik für das patentierte Extrazit. Hierzu wurde Anthrazit-Feinkohle auf drei Millimeter gemahlen, mit Bindemittel bestehend aus 10% Prozent Melasse, ein Rückstand aus der Zuckerproduktion, und 1% Kartoffelstärke gemischt. Dieses Gemenge wurde bei einer Temperatur von 250° C in der Walzenpresse der Fabrik in Briketts in Kissenform gebracht und anschließend silbrig eingefärbt. Die Briketts verbrannten rauchfrei und sorgten für eine wohlige, langanhaltende Wärme.
Quellennachweis:
- Dr. A. Spilker: "Kokerei und Teerprodukte der Steinkohle", Halle (Saale), 1933
- verschiedene Unterlagen des Stadtarchivs Essen zum "Bergwerk Eintracht-Tiefbau"
- "Die Entwickelung des Niederrheinisch-Westfälischen Steinkohlen-Bergbaues in der zweiten Hälfte des 19. Jahrhunderts",
hrsg. vom Verein für die bergbaulichen Interessen im Oberbergamtsbezirk Dortmund, 12 Bde., Berlin 1902-1905, Bd. 9
© Michaela Barz-Berg